Apple, 3d printing, and the future of consumer electronics
- By Paul Rubell
- •
- 02 Dec, 2013
Advanced manufacturing continues to accelerate in adoption. For industry, 3d printing is enabling automation, the fabrication of lighter, longer lasting, and higher tensile parts. From jet engine nozzles (Rolls Royce) to bicycle saddles (Giant), the advent of new manufacturing techniques continues to snowball.
The intellectual property law aspects of 3d printing are another story. Who owns the copyright to an exact-copy of a printed part? Can manufacturing techniques be patented?
Apple has entered the fray.
It has filed a novel patent application for a 3d printing technique designed to fabricate consumer electronics parts using a new alloy, called bulk metallic glass (BMG)
According to the patent filing, the process can create “a telephone, such as a cell phone, and a land-line phone, or any communication device, such as a smart phone, including, for example an iPhone or an electronic email sending/receiving device. It can be a part of a display, such as a digital display, a TV monitor, an electronic-book reader, a portable web-browser (e.g., iPad), and a computer monitor. It can also be an entertainment device, including a portable DVD player, conventional DVD player, Blue-Ray disk player, video game console, music player, such as a portable music player (e.g., iPod), etc. It can also be a part of a device that provides control, such as controlling the streaming of images, videos, sounds (e.g., Apple TV), or it can be a remote control for an electronic device. It can be a part of a computer or its accessories, such as the hard drive tower housing or casing, laptop housing, laptop keyboard, laptop track pad, desktop keyboard, mouse, and speaker. The article can also be applied to a device such as a watch or a clock.”
Parts are manufactured using BMG, layer by layer. A layer of BMG powder is deposited to selected positions and then fused to a layer below by suitable methods such as laser heating or electron beam heating. The deposition and fusing are then repeated as need to construct the part layer by layer. One or more layers of non-BMG can be used as needed. Layers of BMG can be cut from one or more sheets of BMG to desired shapes, stacked and fused to form the part.
From a technological standpoint, Apple’s consumer products may be able to last longer, withstand distress conditions better, and possibly cost less.
From an IP perspective, it is safe to say that the owner of a product also owns 3d printed copies of the product that it builds for itself.
Whether the process should be monopolized by the issuance of a patent is another question altogether.
Science aside — what does this advanced manufacturing technique suggest for the future of building consumer electronics products?
That age-old fear of robots taking jobs away from humans?
Apple sees a path to eliminate its use of low-paid Chinese labor and the bad publicity that accompanies the adverse working conditions.
Is this a good thing?
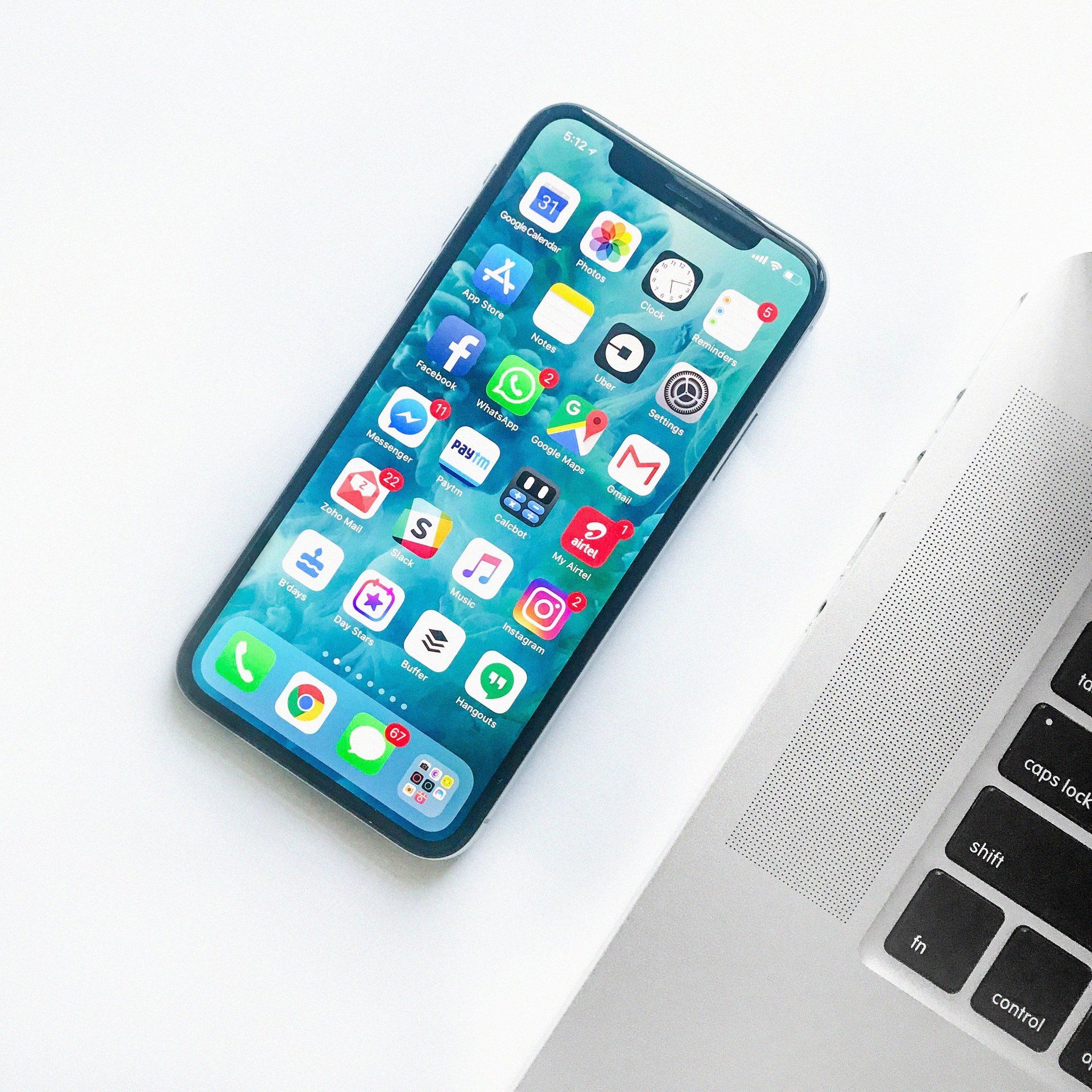
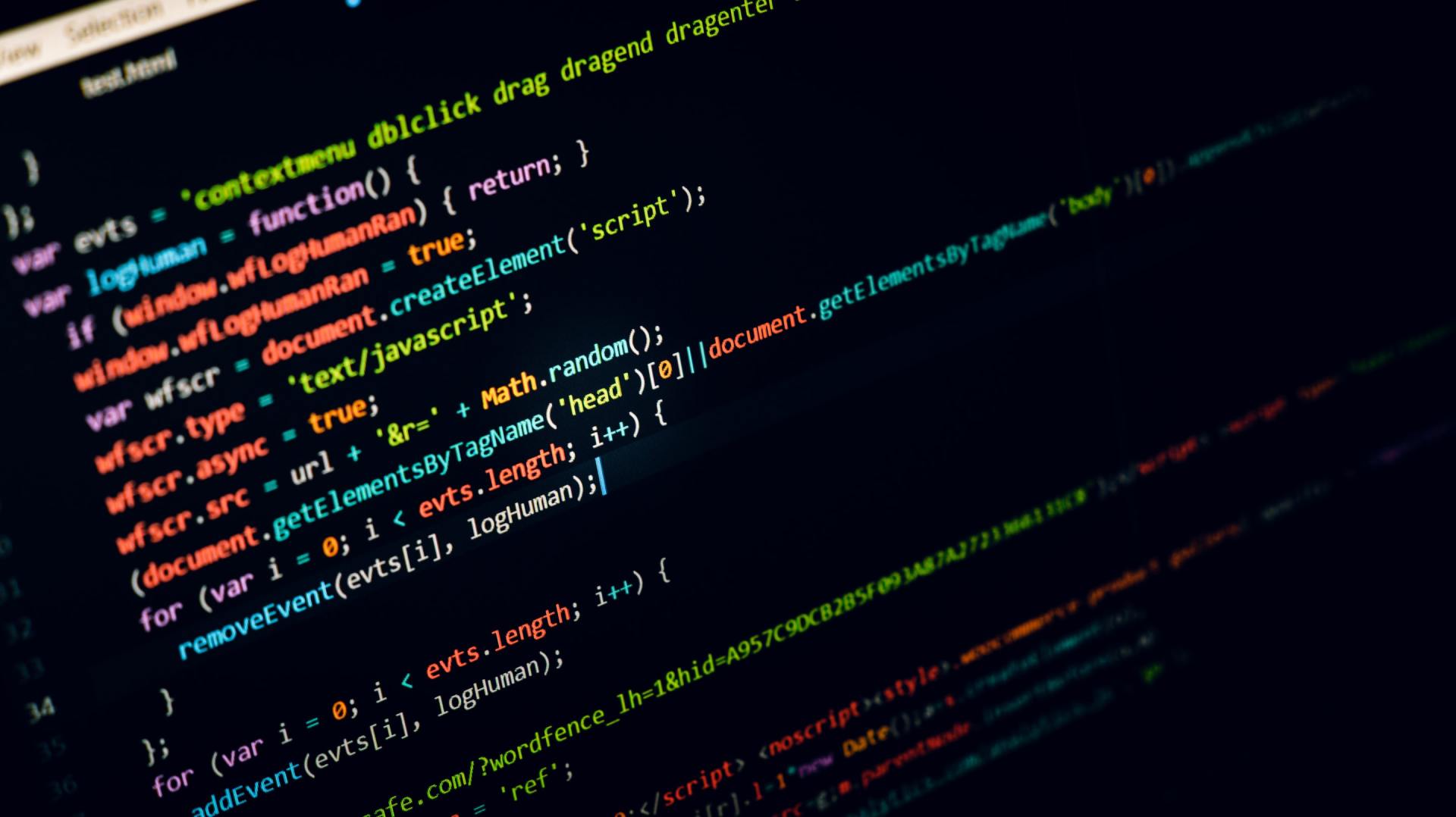
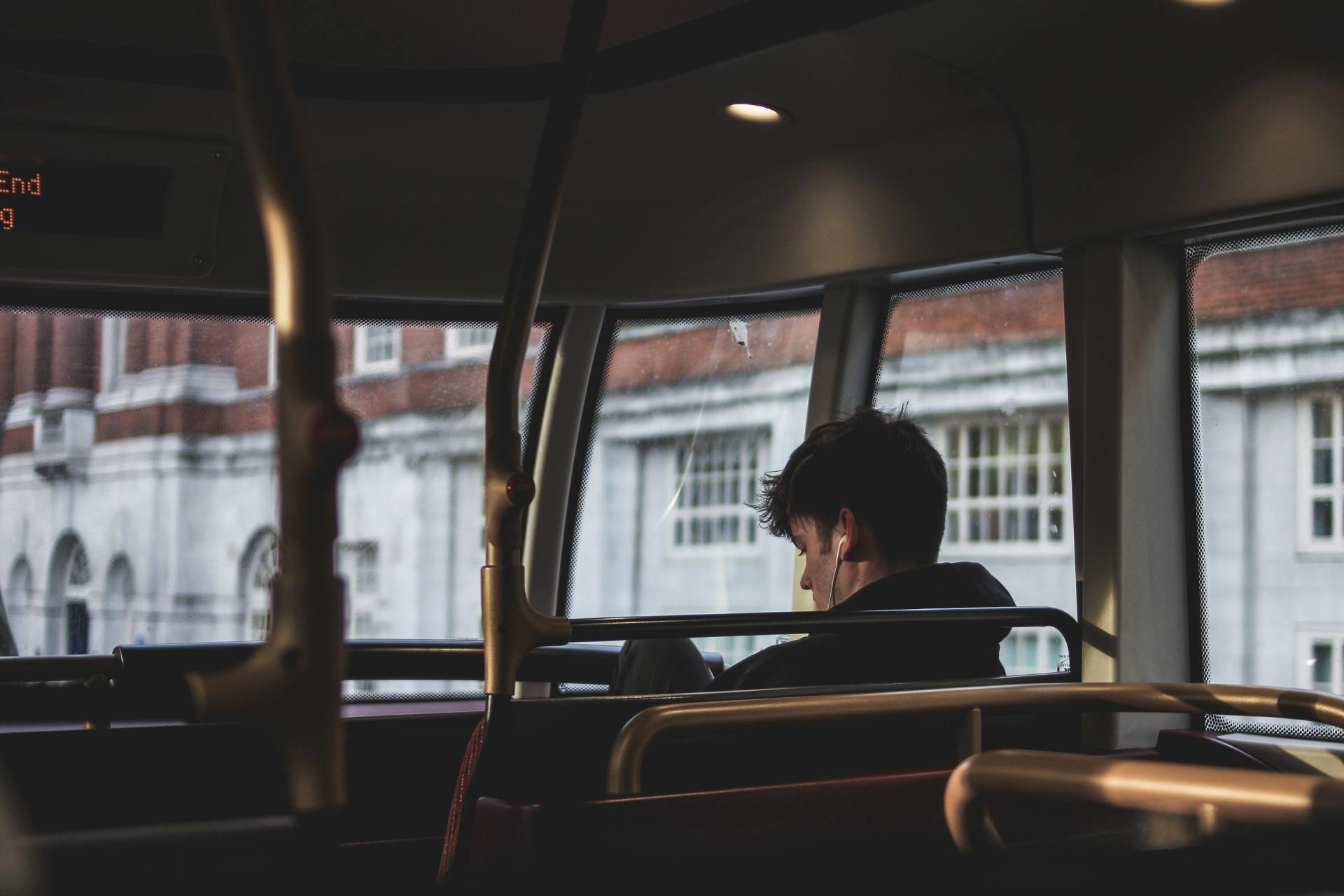
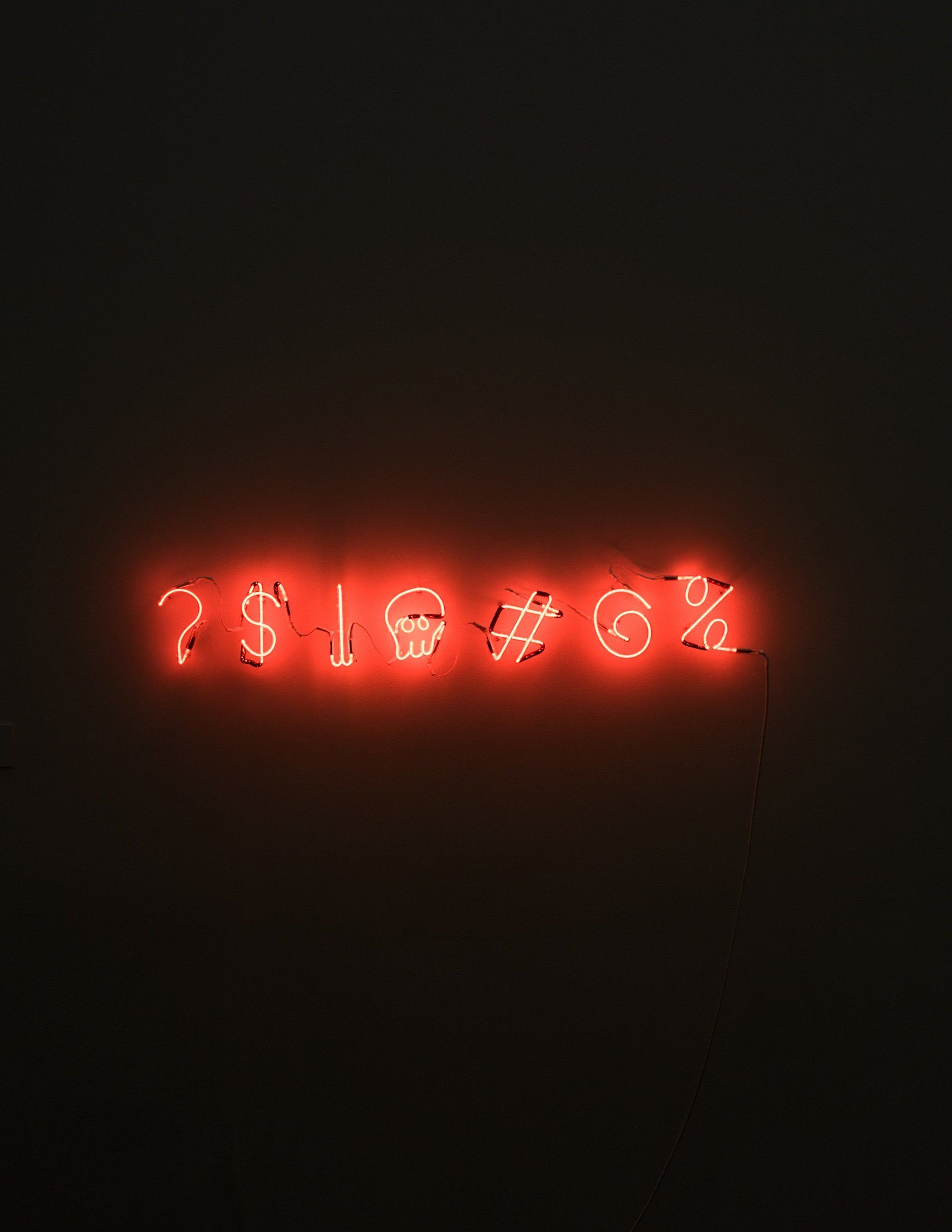
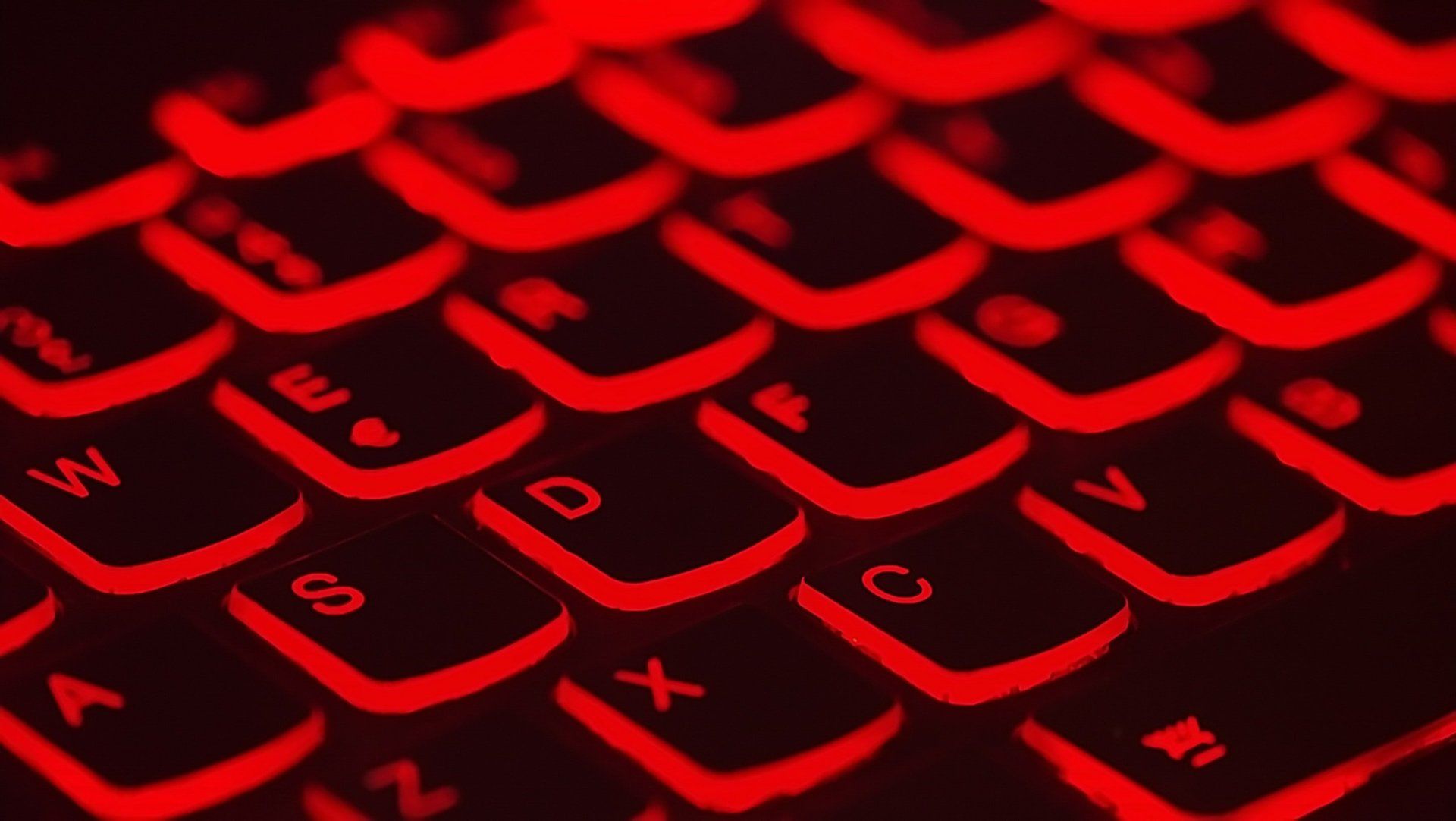
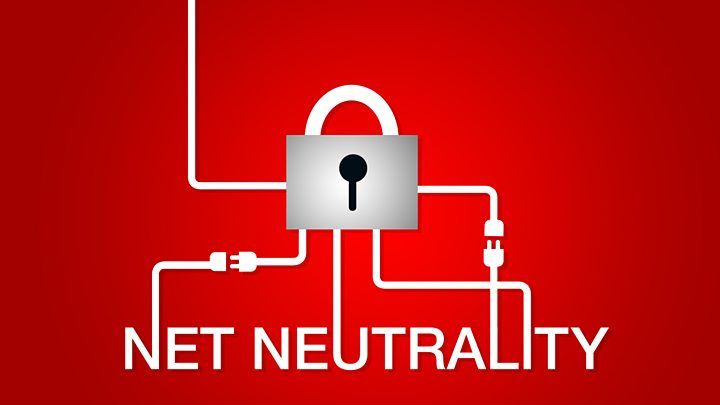
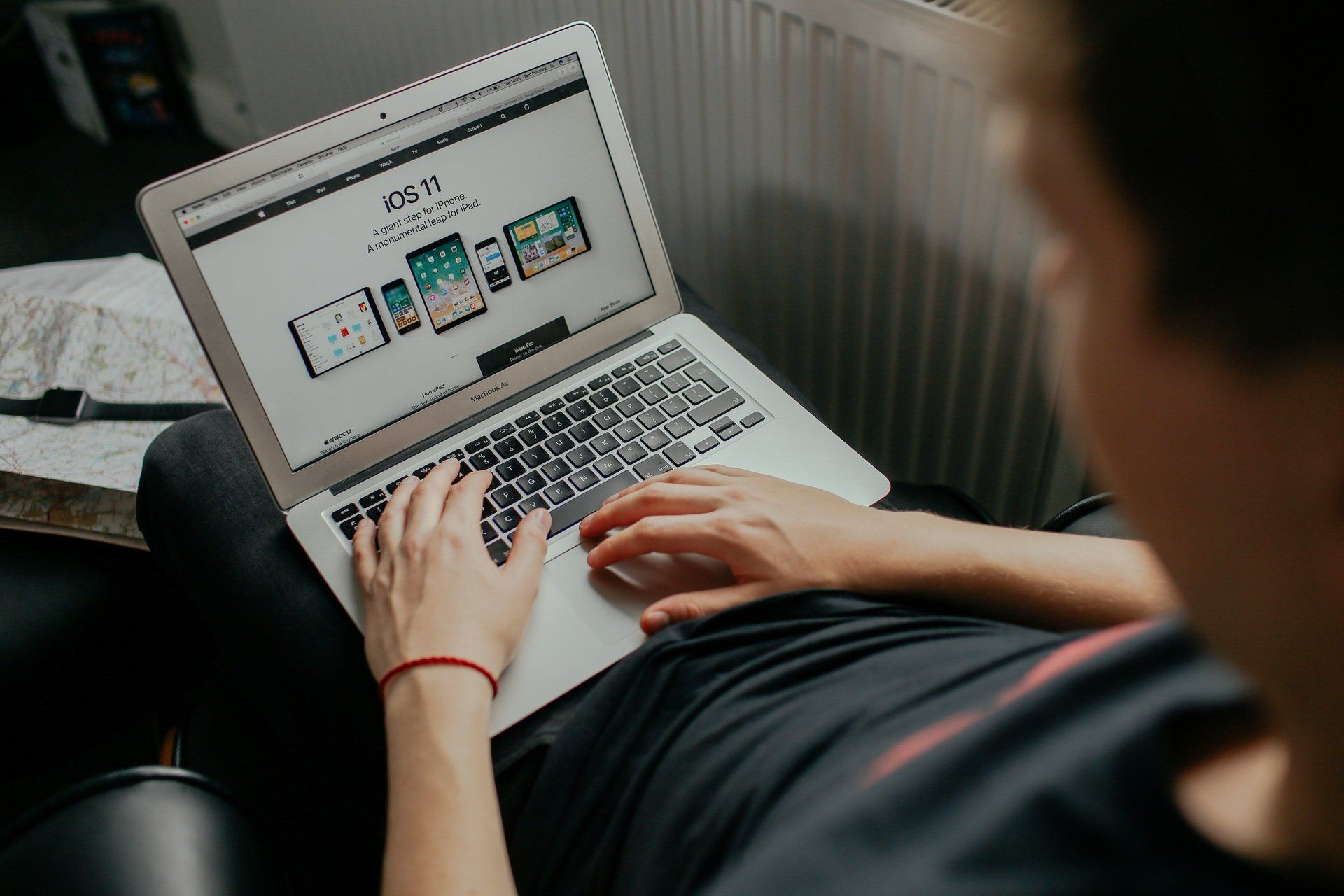